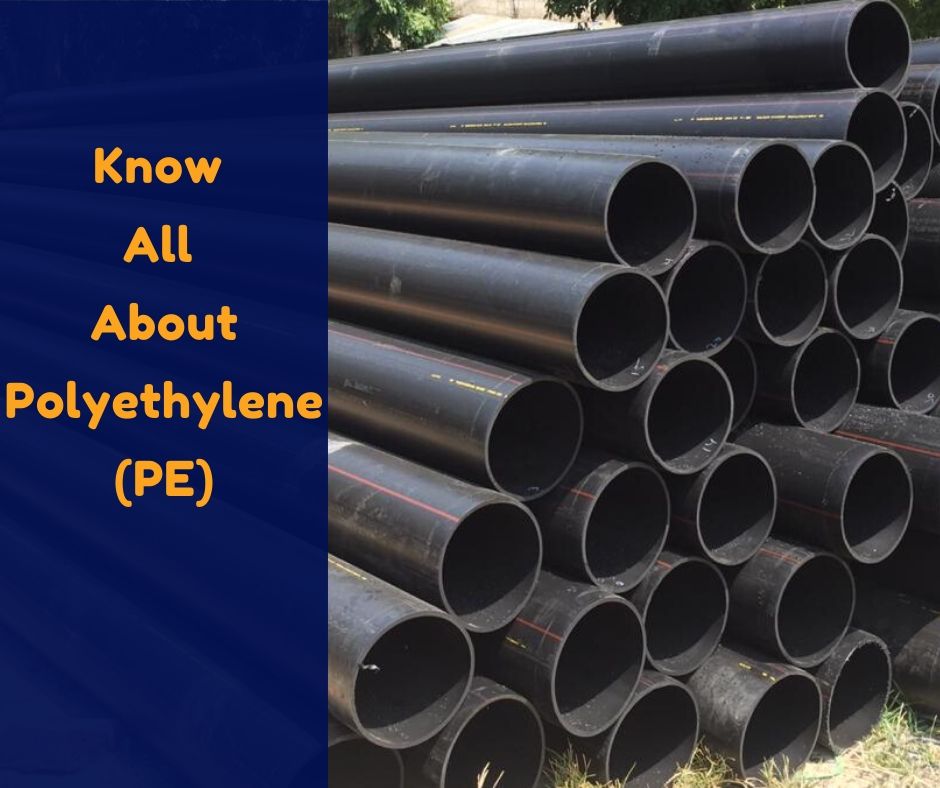
Polyethylene is undoubtedly commonly used and seen polymer in our daily lives. It is also the most common type of plastic that is used in the world today. Everything that we see, from bags, bottles, pipes, toys, etc. are made up of plastics of the type PE. There are also different types of polyethylene, and each type has its own specific use and advantages.
In addition, variations including different branching, density, weight, and crystallinity. As per the manufacture process, different types of polyethylene also have different features, advantages and applications.
Basically, polyethylene is a type of polymer. Polyethylene (PE) is a type of thermoplastic material which is produced from the polymerization of the ethylene material. These types of pipes were first introduced way back in 1930s. However, it started gaining popularity and people started using it since 1950s and 1960s.
Processing of Polyethylene
PE can be processed using various types of techniques like injection molding, blow molding, extrusion as well as other creation processes such as blown film extrusion and calendaring. Different types of processing needs to be implemented to create different kinds of PE products. As this material is ideal for injection modeling, it is commonly used for batch and continuous processing.
Usually, HDPE is manufactured using the process of injection molding, extrusion, blow molding and rotomolding. LDPE is created using extrusion, but injection molding and rotomolding processes are also used. On the other hand, UHMWPE is processed using techniques like compression moulding, ram extrusion, gel spinning, and sintering. Conventional methods aren’t used in this process as this material does not flow at an even rate above its melting point. At present, recycled and green PE are also gaining popularity for processing through 3D Printing. Various types of polyethylene are available in sheer quality, encouraging this material to be used for additive manufacturing.
Recycling and Toxicity
Different types of polyethylene are non-biodegradable in nature and contributes hugely in plastic waste problems. However, PE is a material that can be recycled and used to produce several other useful products such as plastics, bins, and bottles.
Although safe in solid form, PE could be toxic if absorbed in liquid or gaseous forms. Hence, when recycling, all the necessary measures should be taken in order to avoid any sort of harm and hazard to the health of people around them.
Advantages of using Polyethylene
Convenience
Smooth surface of these files also makes them easy to clean and maintain. On the other hand, its lightweight features enables for an easier installation and transportation. Because of these features, PE is a good value for money, is cheaper and is a convenient choice overall.
Strength and Reliability
The moulding technologies which are implemented in creating different types of polyethylene enables strength and robustness. The fact that PE are formed in one-piece structures and absence of welds also helps in adding to its strength.
Polyethylene is also a reliable material which can be used for storing various types of foodstuff and edibles. The storage of various types of liquids can also done in PE bins as they are atoxic.
Durability and Versatility
The materials used in the production of PE offer maximum durability in terms of resisting corrosion and oxidation. Also, due to the use of anti-UV additives, PE products do not deteriorate over time and do not allow any sort of algae formation.
Similarly, PE products can be manufactured in a vast range. Different PE items can be made in various shapes and capacities according to the need. Its versatility also helps in custom installations, where holes and connections need to be made.
Innovation and Safety
PE products are created using various types of innovative and advanced technologies. Due to this, polyethylene items are produced for various sectors including agriculture, boats, storage containers, packaging, safety products, automobiles and many more.
The ease of handling also means that PE products can guarantee absolute safety during the work. In addition, PE products are also 100% recyclable and can be used again and again.
Types of polyethylene
There are different types of polyethylene. All the different types have their own characteristics and is suitable for different types of applications. Here are the details about different types of polyethylene.
High Density Polyethylene (HDPE)
HDPE is a cost-friendly and tough type of thermoplastic. And, it is also manufactured using lower temperature and pressure. This material also has the high density of 0.941 g/cm3. In addition, low amount of branching is present so the molecules are also tightly packed in HDPE.
HDPE offers many impressive qualities like high tensile strength, resistivity, toughness, and translucency. Along with all these, this type of polyethylene that even has desirable insulation properties. On the hind side, this material sometimes tends to crack. It gets affected by UV rays and has a high mold shrinkage as well.
Low Density Polyethylene (LDPE)
LDPE is a comparatively lower density and translucent polymer. It has a semi-rigid structure and is produced under much higher pressure than HDPE. The structure is not as tightly packed, so it isn’t the strongest. However, these types of polyethylene has high ductile strength and lower tensile properties.
Although resistant to acids, alkalis and alcohols, it shows only average resistance to hydrocarbons, mineral oils and oxidizing agents. LDPE also shows high impact strength at lower temperatures.
This polyethylene is also FDA compliant and is popular in food packaging. But, it is also highly inflammable. So we need to take care while using this type of polyethylene.
Linear Low Density Polyethylene (LLDPE)
LLDPE is similar to LDPE. However, it has much shorter branches. These have a higher tensile strength than LDPE and have even replaced them in many applications.
LLDPE is a type of polyethylene that is translucent and has a milky color. In addition, these also have a good resistance and burns without any residue.
Ultra-High-Molecular-Weight Polyethylene (UHMWPE)
UHMWPE has a high molecular weight and has almost has 10 times the molecular weight of HDPE. Due to this, UHMWPE chains aren’t as efficiently packed as in other types of PE products.
However, this is a very tough material and is formed from catalysts and ethylene units. It offers a great wear and cut resistance. UHMWPE products can resist high impacts and corrosion too. This makes them suitable for application such as moving parts, bearings, joints, hip replacements, and even bulletproof vests. Therefore, we can call UHMWPE a high-performance polyethylene material.
Cross-Linked Polyethylene (PEX or XLPE)
This type of polyethylene has high-density cross-linked bonds. Unlike other PE, this is actually a thermoset material and can’t be melted once discarded.
PEX has good chemical resistance and high-temperature properties. It is used in applications such as chemical pipe networks, heating/cooling systems and insulation for high voltage cables.
Here at BN Mahto Group, we have the best HDPE pipes, which are one of the most commonly used type of polyethylene. So, don’t forget to contact us if you have any queries regarding the relative subject matter or if you are looking for the finest HDPE pipes around.